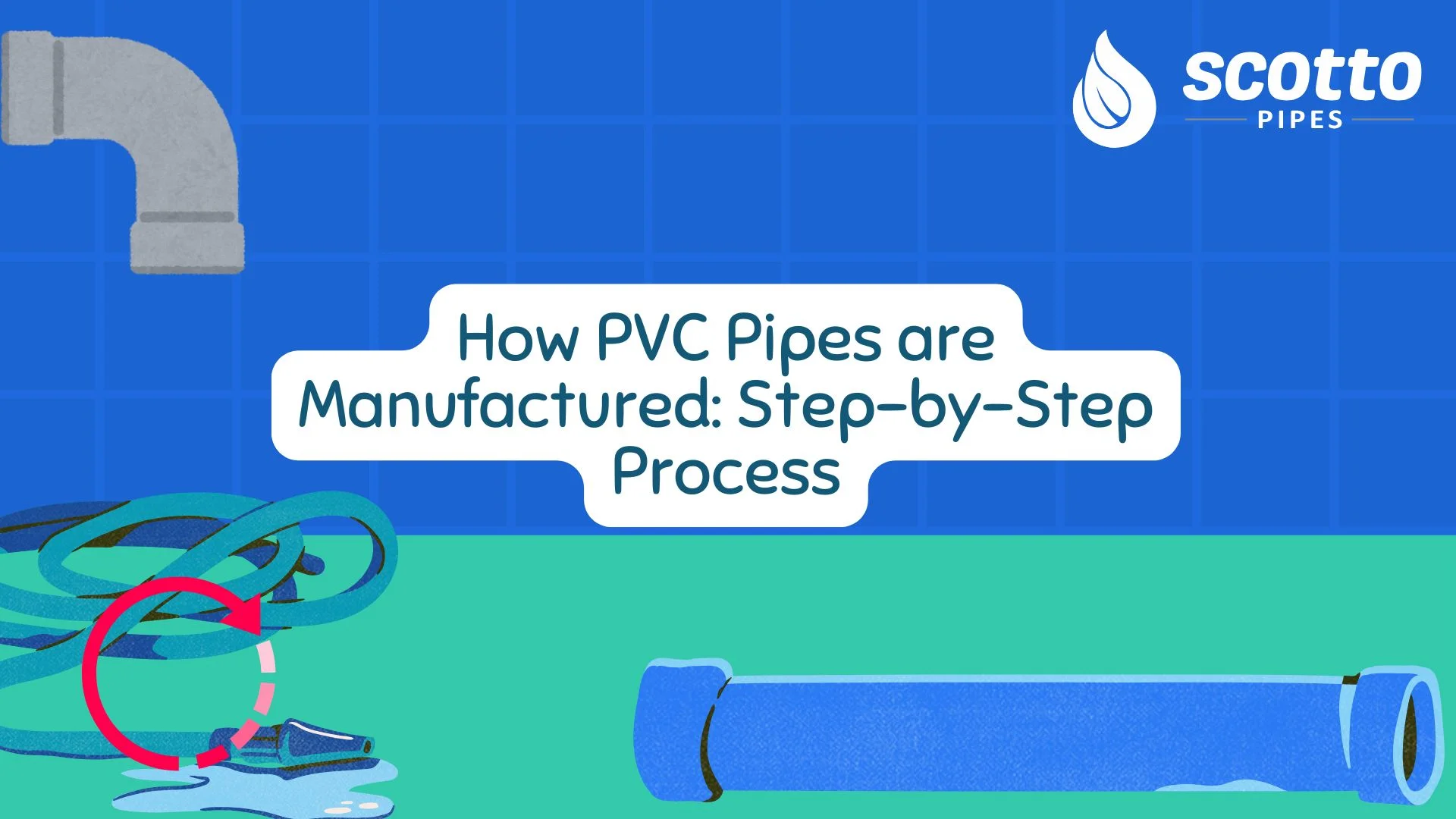
Over the years, PVC (Polyvinyl Chloride) pipes have become irreplaceable in the plumbing, irrigation, and construction industries because they are durable, economical, and resistant to corrosion in most scenarios. PVC pipes are manufactured in an elaborate process that guarantees they are of good quality and last years. In this blog, we will walk through the step-by-step process of making a PVC pipe and explain each step in detail.
PVC Pipes Manufacturing Process Steps:
Step 1: Raw Material Selection and Preparation
Step 2: Compounding and Mixing
Step 3: Extrusion Process
Step 4: Cooling
Step 5: Cutting to Desired Length
Step 6: Printing and Marking
Step 7: Quality Control and Testing
Step 8: Packaging and Storage
Step 9: Distribution and Delivery
Step 1: Raw Material Selection and Preparation
Polyvinyl chloride resin is the primary raw material used in the manufacturing of PVC pipe. In addition to these basic materials, stabilizers, plasticizers, lubricants and pigments may be added to the pipes to improve their properties.
-
PVC Resin: The base material that provides strength and flexibility. However, its lightweight but strong nature makes it appropriate for different uses.
-
Stabilizers: Prevent degradation due to heat and UV exposure. These compounds act as longevity enhancers – especially in outdoor installations of the pipes.
-
Plasticizers: Improve flexibility and durability. They are used to make the pipes more resistant to cracking and breaking under pressure.
-
Lubricants: Aids the smooth processing and prevents sticking to the equipment and thus a smooth manufacturing process takes place.
- Pigments: Provide color to the pipes as per requirements. It also helps in identifying pipes for such applications.
Step 2: Compounding and Mixing
In this stage, the raw materials are combined to become uniformly mixed. In this mixture high-speed mixer as both heated and blended to ensure even dispersion of additives within the mixture. The cooled and stored compound for further processing is then well mixed. The final quality of PVC pipes depends on the quality of mixing of concentrates used to produce them.
Step 3: Extrusion Process
PVC pipe manufacturing heart is extrusion. We proceed as follows in the process:
-
Feeding the Material: The material, blended PVC compound is fed to an extruder through a hopper. The controlled rate of feeding is to keep the production steady.
-
Homogenization and Melting: In the extruder, the material is heated by electric heaters and mixed mechanically with rotating screws. It ensures uniform melting and no defect in the final product.
-
Shaping Through a Die: The molten PVC is forced through a specially made die that when shaped, forms a cylindrical pipe. It is important to note that the die design has an important role to play with regard to the thickness and size of the pipe.
-
Hot Extruded Pipe: Hot extruded pipe passes through a sizing sleeve & vacuum calibration tank for the diameter & thickness sizing. This step is to be sure that the pipes comply with certain dimensions.
Step 4: Cooling
After the pipe is formed, it has to be cooled to ensure its structural integrity. Thus, with a water cooling system, the pipe passes through a bath or spray chamber of water. Thermal stability is assured, as determined by rapid cooling and prevention of warping. The cooling must be proper to avoid cracking or weak areas in the pipe and prevent the formation of internal stress.
Step 5: Cutting to Desired Length
Once cooled, the pipes find their way to the cutting unit where they are cut to the sizes required — often as standard size of 3m, 6m, or according to industry demand. Since high-precision tools are used during the cutting process, clean edges are guaranteed and the lengths will be uniform, making installation a piece of cake.
Step 6: Printing and Marking
The pipes are then passed through a marking station where essential information such as:
-
Pipe diameter and thickness
-
Manufacturer’s name and brand
-
Batch number
Industry standards compliance is printed using inkjet printing technology. These markings are crucial for traceability and ensure compliance with industry regulations. Marking also helps users identify the right pipe for specific applications.
Step 7: Quality Control and Testing
Quality assurance is a crucial part of PVC pipe manufacturing. Several tests are conducted to ensure that the pipes meet industry standards and perform well under different conditions.
PVC pipe manufacturing involves quality assurance. After constructing them they perform several tests to ensure they meet industry standards and will work under other conditions.
Common Tests Include:
-
Dimensional Testing: Required for uniformity of a part in size and thickness for proper fitting and connection.
-
Internal Pressure Test (or Pressure Testing): Tests whether the pipe could withstand internal pressure without bursting. It is especially useful for plumbing and irrigation use.
-
Test of Impact Resistance: Ensures durability to external forces. Mechanical impact on pipes must be tolerated during transportation and installation.
-
Tensile Strength Test: Measures the pipe’s strength and flexibility. It has sufficient high tensile strength to withstand external stress without deforming the pipe.
-
Chemical Resistance Test: Verifies resistance to corrosive substances. This is very important when the pipes are exposed to chemicals that are used in industrial applications.
Step 8: Packaging and Storage
Once the pipes have met quality standards, they are bundled, wrapped, packed, and stored, until transport arrives. It protects through packaging from damage during handling and shipping. Transportation of pipes in bulk and storage in warehouses have been the regular practice to ensure efficient distribution. Sometimes, the pipes are also protected with protective films to prevent scratches as well as level of contamination.
Step 9: Distribution and Delivery
The last step involves spreading the pipes among industries, construction sites, as well as plumbing suppliers. It is widely used in residential, commercial, agriculture and probably anywhere that you’ll find water pipes. Pipes are delivered to the market on time and available with the help of reliable transportation and logistics.
Scotto Pipes - Leading PVC Pipes Manufacturer
Scotto Pipes is a cutting-edge PVC pipes manufacturer & supplier that has earned a name for its excellent quality products. They have a variety of pipes at their disposal from UPVC pipes, rigid PVC pipes, garden pipes and suction pipes. Scotto Pipes sets its customers with a commitment to innovation and quality, making sure that the products produced fit in all senses of the word durability, strength and efficiency. Scotto Pipes supplies reliable solutions whether for plumbing, irrigation or industrial applications.
Conclusion
PVC pipes are manufactured by a highly systematic and quality orientation manufacturing process involving methods that yield durable, reliable and cost-friendly pipes. In modern times, manufacturing production is done in an improved way that increases its efficiency and the quality of the product, hence why PVC pipes are selected for use in many places.
If you want PVC pipes of super quality, then look for a manufacturer that determines stringent quality standards and testing procedures for good performance and durability.