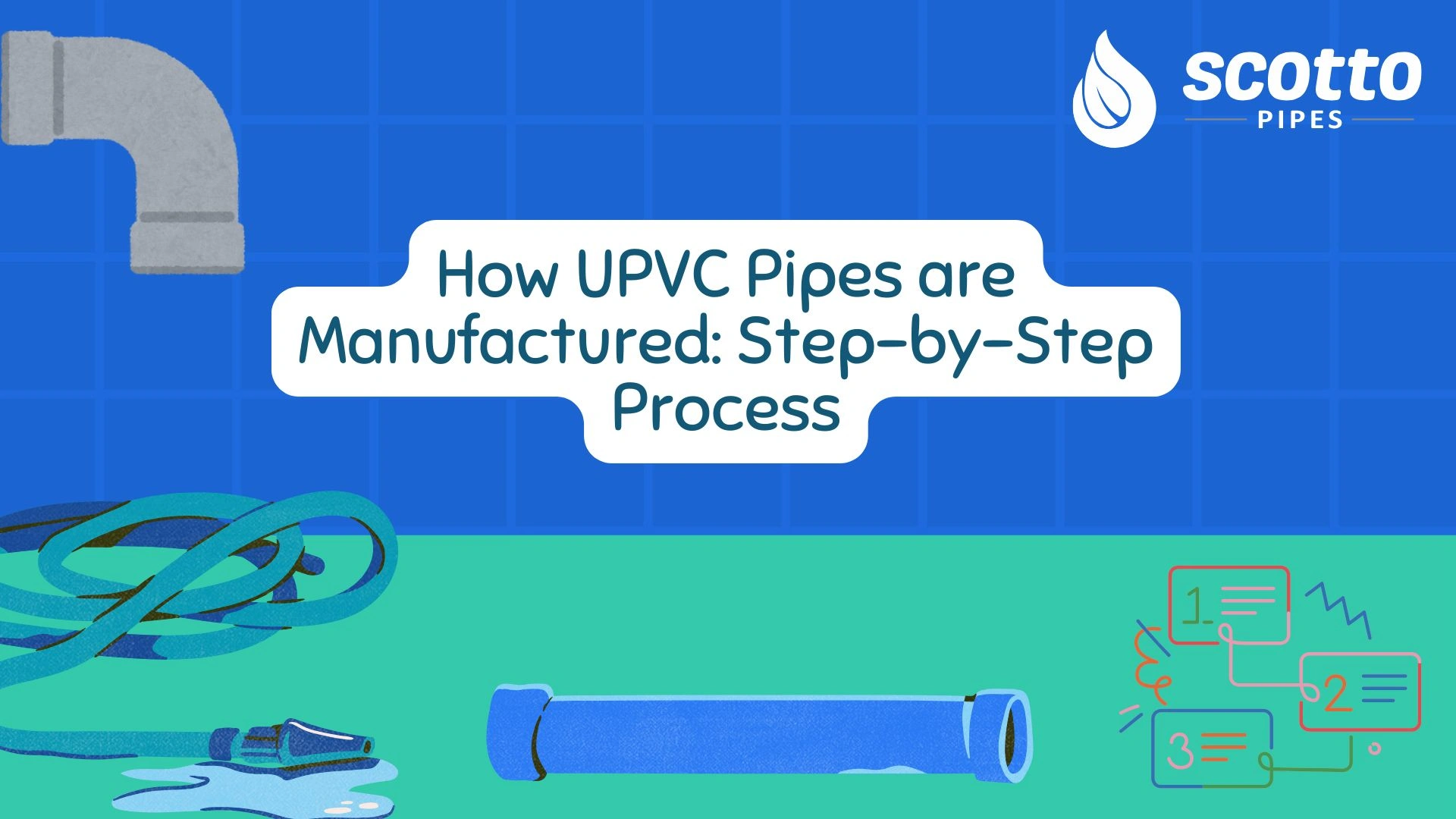
The Unplasticised Polyvinyl Chloride (uPVC) pipes have witnessed unprecedented growth in use in plumbing, irrigation, and as infrastructure solutions because it is strong, non-reactive and durable enough to have a long service life in place. So if you are interested in how these trusted pipes are made in here's a complete pick of the uPVC pipe manufacturing process.
How UPVC Pipes Are Made: A Complete Guide
Unplasticized Polyvinyl Chloride (UPVC) pipes are widely used in plumbing, drainage, and irrigation systems due to their durability, chemical resistance, and low maintenance. Here’s a step-by-step guide to the UPVC pipe manufacturing process:
Step 1: Raw Material Selection and Blending
Everything starts with the selection of a high quality PVC resin. Manufacturers blend the resin with different additives to improve performance and satisfy the application’s needs.
- Thermal stabilizers: to prevent degradation during high temperature processing
- Flow lubricants: to improve flow and surface finish
- Impact modifiers: To increase the mechanical strength
- Fillers like calcium carbonate: Calcium carbonate fillers to increase rigidity and decrease costs
- Pigments: for color and UV protection
Step 2: Mixing and Compounding
In a high speed mixer, these ingredients are mixed to form a homogenous dry blend, called PVC compound.
- High Speed Mixing: The UPVC resin and additives are mixed at high speed to get the precise proportions. This sleeves in uniform material distribution and homogeneity.
- Heating: The mixture is heated and homogenized to form a ready to extrude compound. It improves flowability and guarantees constant quality.
Step 3: Material Feeding and Melting (Extrusion Process)
The dry blend is dumped into a twin screw or single screw extruder and is heated and plasticized before being extruded. The screw in the extruder that rotates pushes the material forward and the heating of the compound progressively raises the temperature to produce a viscous, slightly more uniform flow.
- Temperature zones: Maintained within a controlled slightly variant zone of 160°C – 200°C
- Screw configuration: Designed for maximum melting and minimum degradation.
- Fills for degassing: Removes air or moisture trapped in your concrete for better consistency
Step 4: Pipe Formation Through Die and Calibration
Once molten, the uPVC passes through a pipe die head, where it’s shaped into a cylindrical pipe. The freshly extruded pipe enters a calibration unit and vacuum sizing tank which ensures the pipe’s outer diameter and wall thickness conform to standards.
- Vacuum sizing: Maintains precise outer dimensions and surface smoothness
- Die design: Adjusted for various pipe sizes (20 mm to 315 mm and more)
- Wall thickness: Varies by application – higher for pressure pipes
Step 5: Cooling in Water Tanks
The hot pipe is immediately passed through cooling baths containing chilled water, which solidifies and preserves the shape of the pipe. Uniform cooling is assured without warping or distortion through these tanks.
- Spray-type or immersion cooling
- Gradual, controlled cooling in multi stage tanks
- Provides crystallinity for improved strength and thermal stability.
Step 6: Haul-Off (Pulling System)
When cooled, the pipe is pulled through the extrusion line by a haul off or caterpillar puller. This step helps ensure optimized speed and tension, preventing elongation or deformation.
- Rubber belt or chain traction
- Smooth pulling is maintained by variable speed drives.
- For line balance, synchronised with extruder speed
Step 7: Cutting and Length Control
The pipe moves on to the automatic cutting unit, where it is cut to standard lengths (usually one of 3m, 6m or 12m). Instead, length is detected by advanced machines and they trigger precision cutting through sensors.
- Automated cutting machines: Pipes are cut to standard or customized lengths.
- Marking: Specifications such as brand name, size, type, etc., are printed or embossed on the pipe surface.
Step 8: Quality Testing and Assurance
It is crucial that the process be controlled in quality. It is tested at different stages to meet the national & international standards (IS, ASTM, DIN etc.).
- When the resin and additives meet the required specifications.
- Parameters of interest such as temperature, pressure and extrusion speed are closely monitored.
- Physical and mechanical tests (pressure resistance, strength, flexibility) are performed to demonstrate compliance with industry standards.
- Pipes that pass all tests are only allowed to move on to packaging.
Step 9: Marking, Packaging, and Dispatch
Approved pipes are laser-marked or ink-jet printed with essential information:
- Brand name and logo
- Pipe diameter and class (e.g., Class 2, Class 3)
- IS or ASTM standard number
- Batch number and manufacturing date
The pipes are bundled, shrink wrapped or strapped and stored in clear, shady areas to protect from weather exposure.
Applications of UPVC Pipes
UPVC pipes serve diverse purposes across industries:
- There are various uses of UPVC pipes across various industries.
- Systems used for plumbing of residential and commercial buildings.
- Sewage systems for wastewater management.
- Industrial pipelines for chemical transport.
Final Thoughts
The uPVC pipe manufacturing process is a blend of precision engineering, material science, and quality control. Each step is designed to create products that are safe, strong, and built to last. From water supply systems to industrial piping and agriculture, uPVC pipes have become an integral part of modern infrastructure.
At Scotto Pipes, we ensure every pipe that leaves our facility meets the highest standards of quality and performance. Backed by advanced technology and stringent testing protocols, our uPVC pipes deliver lasting value for every application.